CASE STUDY
Detectronic specialises in monitoring and managing sewer and wastewater networks. The company has a rich history of working with water utilities to facilitate the real-time monitoring of water flow, levels, and quality. They do this by monitoring wastewater flows and effluent levels at CSOs and other critical points in the network.
Key Highlights
Before we rolled out the solution from Binary Forge, we still used some very manual processes.
With the team's expertise in helping us implement an end-to-end solution that's both futureproof and user-friendly, we have saved a considerable sum in not only labour costs but through the reduction of error and subsequent re-work.
In addition, the time taken to plan and then schedule a job has been reduced by around 73%, and data accuracy has increased significantly, allowing us to release data to our customers within a much shorter timeframe. Engineers are getting more done in less time; our teams are free to do more critical work, representing an excellent win for our customers and teams.
We would absolutely recommend Binary Forge.
Client Challenges
Our Client needed to solve a growing issue of an admin burden, eradicate the potential for erroneous data being gathered from the field and use more reliable, secure systems to support the allocation and completion of their pre-install surveys.
Inefficiencies in job creation and scheduling
Jobs were assigned manually through a combination of multiple spreadsheets and raw data collected from third-party sources.
This represented a costly administration burden for teams in the back office. Staff would collate different Excel sheets to schedule work from multiple fragmented information sources, leading to duplication of work and confusion. Yet rapidly changing schedules meant they often had to repeat jobs.
Manual data entry with no control
Field engineers would collect their daily work schedules by downloading multiple spreadsheets from specific folders onto laptops from a third-party file sharing site. The Engineers would then attend their assigned jobs installing Detectronic’s monitoring hardware within the wastewater systems.
Data about the day's installations was collected and input into various spreadsheets before being uploaded along with site photos to the file sharing site to be manually processed by the back-office team.
No integration and multiple manual touchpoints
In addition to installation and maintenance work, Detectronic undertakes site surveys before installation for themselves and third parties. The data collected in these surveys was not automatically integrated into the Detectronic systems and added further overhead in terms of planning and processing for the back-office teams.
Business-critical risks
The inventory information relating to each installed monitoring device must be accurate. Failure to correctly record the location information could lead to alerts being raised at the wrong or an unknown site. Alternatively, if the installation process is not followed correctly, devices may not have been commissioned and would return no data requiring additional visits at Detectronic’s cost.
Poor data quality
Ultimately, poor data accuracy could lead to additional costs and reputational damage for the company.
THE SOLUTION
In just a few months, Binary Forge worked to deliver a solution to overcome Detectronic's critical issues - the most pressing being the risk of error in data reported through existing processes and the reduction of wasted costs through inefficiencies in the back office when handling data and arranging site work.
Working with the team at Detectronic, Binary Forge analysed the existing process flow and proposed a new integrated solution covering all aspects of the business process from the back-office team to the users in the field.
Mobile Application
SaaS Management Platform
System Integration
MOBILE APP
Providing the field service engineers with a mobile application, which can be installed on a tablet or phone, and which dynamically adapts to the data collection requirements of the installation. The site engineers complete only the required information, can be sure they have signed off a site correctly and no longer have the overhead of managing the uploading of multiple spreadsheets and photographs. Due to the data collection mechanism, the possibility of entering incorrect data has been significantly reduced.
SYSTEM INTEGRATION
To maximize the potential of the new platform, Detectronic needed to integrate the data collected during site visits with their operational data warehouse.
Our team tackled this challenge by developing a customised API that seamlessly integrates data from the new platform into their existing system. This solution realised another improvement in data input efficiency and eliminated an additional risk that could arise from manual data entry.
SaaS
A Software as a Service (SaaS) Management Portal manages users and jobs within the process flow. Automating tasks previously completed manually whilst adding data verification, checks and auditing.
These tools enable the teams to schedule field engineer jobs months in advance but still offer the flexibility to react to changing priorities daily. The Portal offers a suite of simplified reports to allow the back office to monitor progress and measure performance against KPIs.
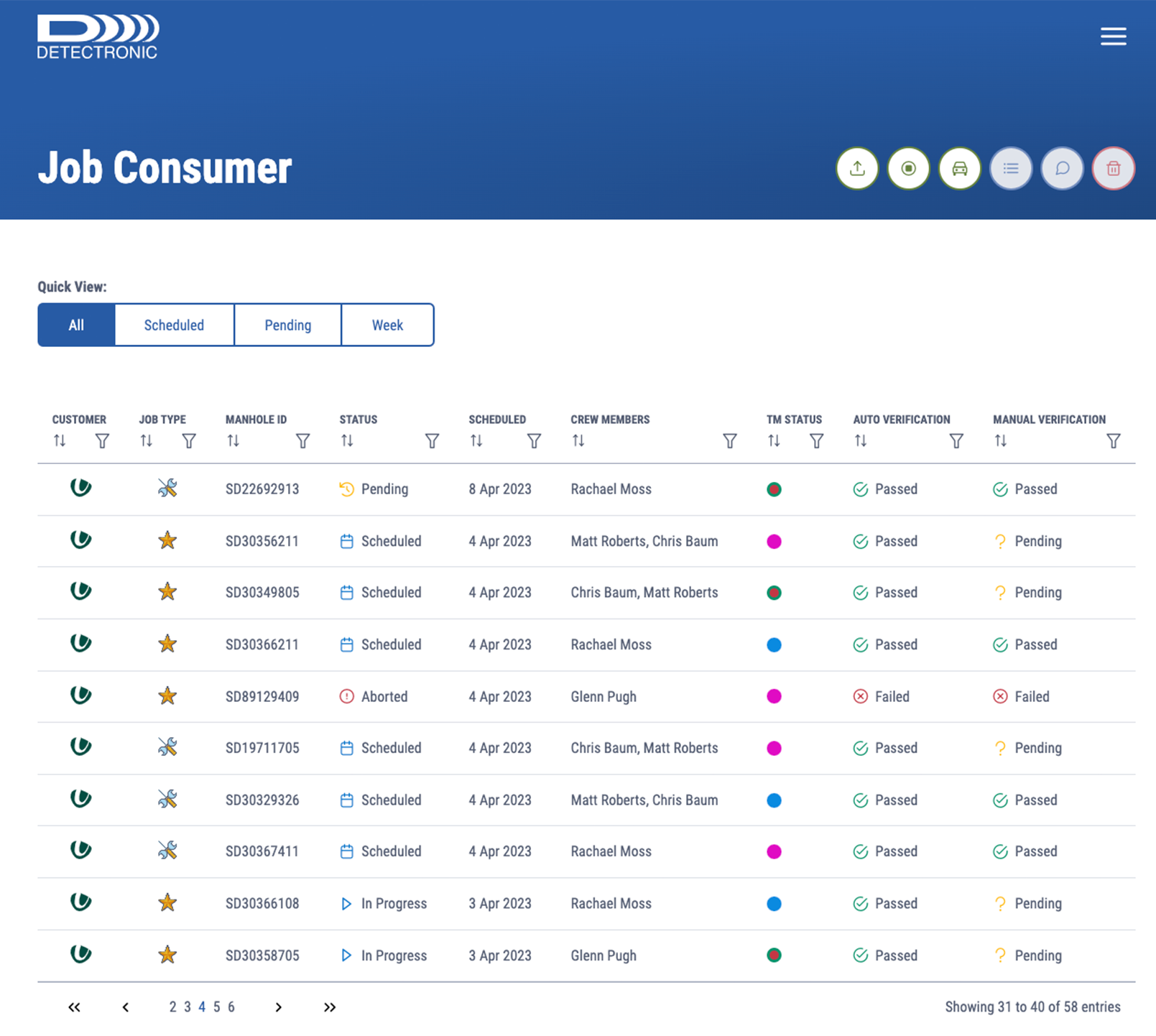
RESULTS
Improvement in data accuracy
By providing predefined responses for the field engineers and dynamic input forms based on those responses, data accuracy has been improved.
Reduction in back-office processing
Using the Portal, the back-office team can easily upload job specifications without duplicating data and identify available teams to schedule the job.
Process automation
Automating tasks such as data verification and propagation reduces the manual overhead for the Detectronic team members and helps ensure the quality of data in the system.
A joined-up solution
Everything from new installs, maintenance visits and pre-install inspections are now designated as a job per crew. Engineers automatically receive the days jobs, capture all the data, and it is automatically pushed into the database for a seamless approach.
Enhanced auditing of jobs and crews
Requiring users to authenticate ensures Detectronic knows who worked on which jobs and by collecting additional metadata when and where those jobs were recorded.
Future-proof systems
The solution can be extended to include additional functionality through integration with the field service app or by utilising the Portals API.